As concerned as possible to retain its customers, sometimes more concerned than to acquire new ones, LINT TOP has for some time been investing a lot of means and efforts to ensure the most complete training for its various customers, because the primary objective of LINT TOP is not to sell production equipment only, but also is above all to support all its customers in the various processes of using the various equipment sold.
The principle followed by LINT TOP can be explained as follows: By making its customers experts in the use of their various acquired equipment, LINT TOP thus develops assured and lasting manner, their satisfaction and their attachment to the brand.
It is indeed the use of the equipment itself that determines its true value, therefore, LINT TOP works tirelessly to apply this principle and ensure that all its customers learn to use and master various equipment acquired, learn how to maintain them and adapt them to their multiple needs.
LINT TOP has understood this concept very well and is doing everything to implement it in the most efficient way possible with all its customers.
For example, we can cite the case of one of our customers in Tunisia who will soon proceed to the reception of several equipment that he has ordered and which concern the production of tinned copper cables for photovoltaic cells of different sections. as well as low voltage copper power cables of different sections too.
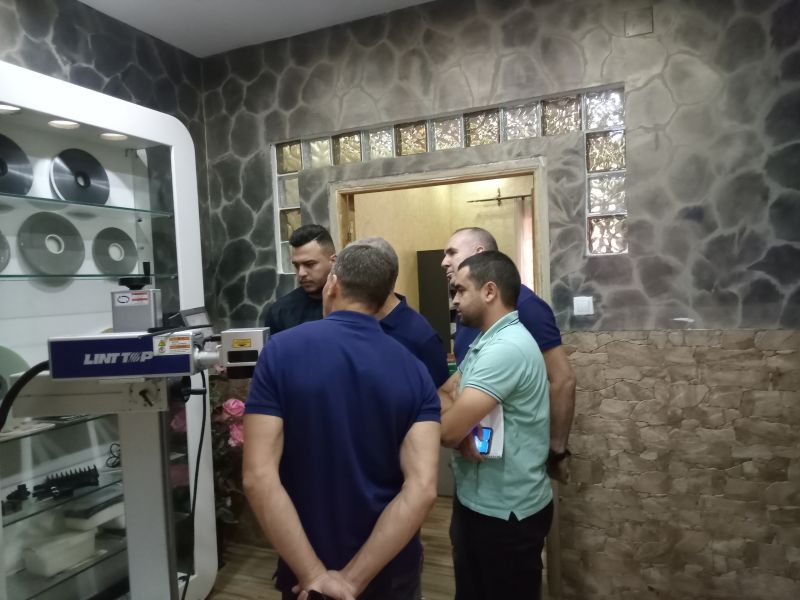
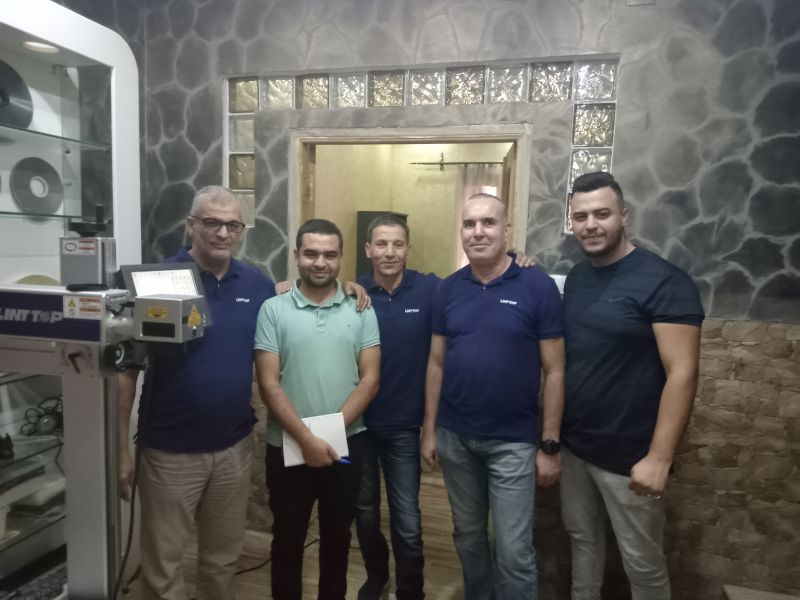
This turnkey project supported by LINT TOP is the first of its kind in all of southern Tunisia and LINT TOP ensured the supply of all the needs necessary for the realization of this project namely:
1 - Production equipment:
- 17 dies copper medium drawing machine with annealer and
spooler (Z17 Drawing machine + T2000 Annealer+ K200 Tension controller + S630 Spooler)
- 22 dies copper fine wire drawing machine with in line continuous annealer (Drawing unit + annealer + Steam generator + spooler )
- 630 bunching machine (used for the multistrand twisting of bare copper, coated tin, coated silver, copper-clad aluminium wire, enamelled wire, and other special alloy wires)
- 1250 bunching machine (Twisted cross-sectional area: hard structure 4-35mm² soft structure 4-50mm²)
- 70+35 extruder high speed insulation line (Extruding material PVC, XLPO, XLPE - Conductor cross section from 1 mm² to 25 mm²
- 90 extruder for sheathing layer, complete line (1250 single head shaftless power payoff + 1.5m vertical tension frame + Powdering machine + Straightening toolbox + φ90 extruder including two sets screws+ Adjusting deviation square crosshead (S136) + Drying suction machine (200KG) + 2m movable water tank + Water blowing device + Outer diameter gauge + High-speed printer + 600 auxiliary traction slewing box + double layer water tank + φ700mm double-wheel tractor + 12M horizontal type wire storage frame + 15kV Industrial frequency sparker tester + φ1250mm double-head shaftless takeup)
- 1246 Automatic coiling machine w ith full seal thermal shrinking used for cable automatic coiling, binding, and labeling machine
- Semi-automatic coiling machine
2 - Test equipement :
- DC resistance testing of conductor Immersion voltage test for finished cables (6.5kV,5min) - Insulation resistance test - Insulation resistance test - Outside diameter measurement (conductor, insulation, sheathing) - Thickness measurement (insulation, sheathing)- Single cable burning test - Tensile strength and elongation at break tests before and after ageing (insulation, sheathing) - Thermal elongation test - LTG-300L laser marking machine
3 - Auxiliary equipment :
- ABS250 plastic bobbin - PND630 double layer high speed metal bobbin - ABS800 plastic bobbin - ABS1000 plastic bobbin - PND1250 high speed metal bobbin - Air compressor LT22-8GA - Air cooled chillers - welders for different wire diameters - filters for drawing emulsion etc...
As soon as the shipment of the equipment was made from China, the engineers of our branch LINT TOP AFRICA CENTER immediately took charge of the training of a technician from our client at our branch in Algeria spread over several days.
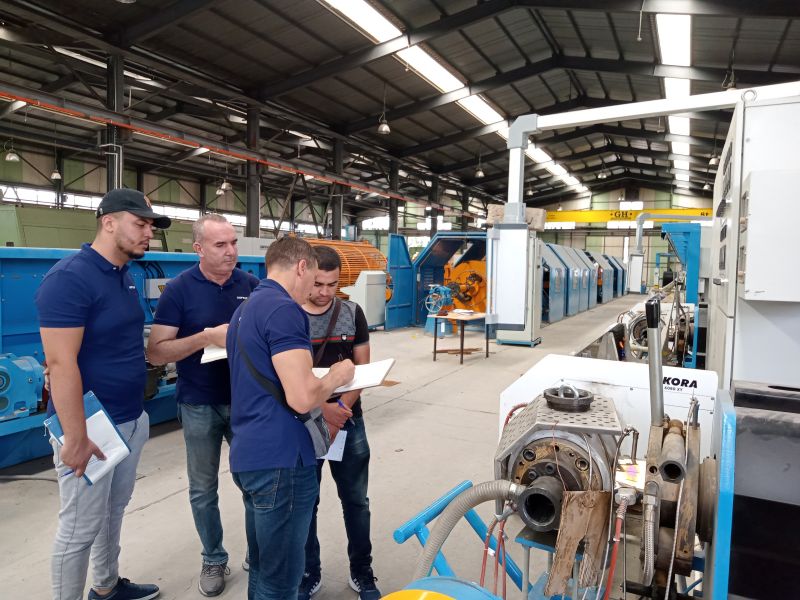
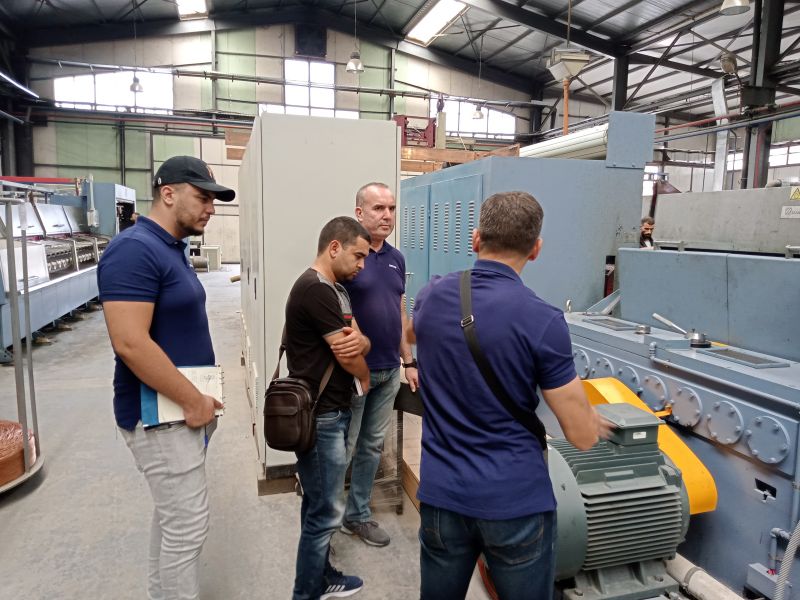
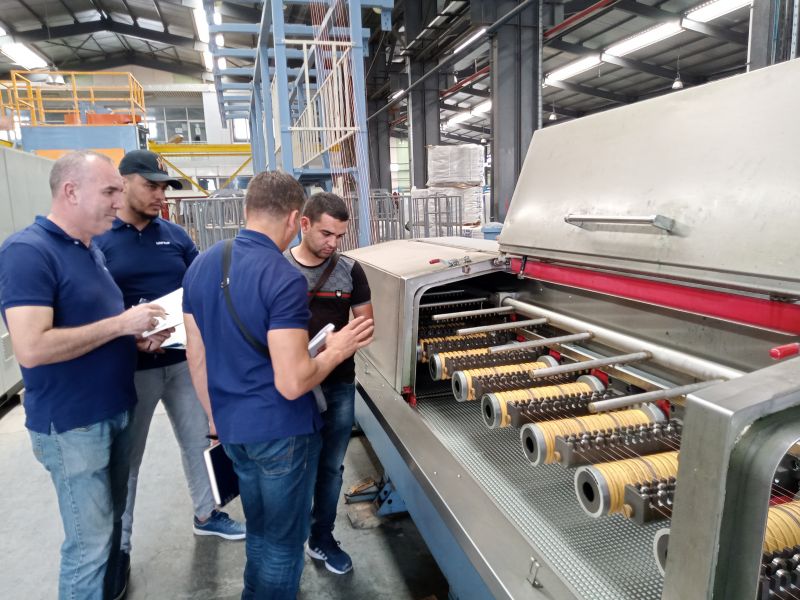
The training program given to our client was as follows:
- Step 1: Visit of one of our partners in Algeria, user of our equipment for the production of low voltage copper energy cables. During this visit, the technician of our Tunisian customer was able to discover and supervise production equipment in operation, similar to those which he will have to use on the level of his factory in Tunisia.
- Step 2 : Basic training on the operating principles of each production equipment.
- Step 3 : Training on the basic principles concerning the assembly operations of equipment, all aspects relating to its operation have been reviewed, namely, the follow-up of the construction of the ground foundations of the equipment, the alignment of the parts of the production lines, the assembly of the different parts of the production lines, internal and external electrical wiring, fixing parts of production lines etc..
- Step 4 : Basic training on the product range that the customer is going to manufacture, construction of the conductive cores, structures of the insulating layers, the inner sheaths and the outer sheaths, assembly of the conductors, etc....
- Step 5 : Review of the various standards and specifications in force concerning the customer's entire production range.
- Step 6 : Initiation to the various manufacturing processes, drawing, strainding , assembly, extrusion etc..
- Step 7 : Initiation to the various quality control processes: Raw material reception control, in-process control and finished product control
- Step 8 : Initiation to the process of preventive and curative maintenance of the various production equipment
- Step 9 : Theoretical and practical training on the function of laser printers.
Train its customers well to retain them well, one of the key strategies of LINT TOP.